|
上海武田机电,总部设在上海,在香港,德国,美国,日本均设有分公司,拥有良好的购销渠道,欢迎来电咨询 TEL:0086-21-51085793 |
|
|
|
|
|
|

国际工业装备采购中心
上海武田机电公司,是专业的欧美及日韩进口工业产品提供商。在欧洲,美国,日本及韩国拥有良好的渠道与深厚的关系,代理及经营多种品牌工业产品,欢迎选购。
|
|
|
武田机电
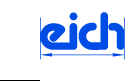
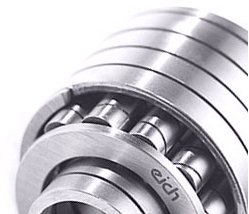
EICH轴承,EICH轴套,EICH轴承,EICH花键
Use of Eich bearings in continuous casting plants. The Eich name has been closely associated with the international steel industry since the 60s owing to the success of the eich roller bearings in continuous casting plants. Eich bearings equipped with the typical spring bushings were installed to meet the demand for a dust-resistant bearing for the strand guide in the upper segments. The Eich bearings were installed both as original equipment and as replacements for the bearing variants used up to that time with solid fixed bearing rings. In 1967 Eich bearings were installed in a GrilloFunke plant as part of its original equipment. Standard roller bearings have a relatively large diameter and therefore require larger roller diameters for the strand guides. In the upper segments of the strand guide, this can lead to a risk of bulging of the elatively thin strand shell. The bearing installed in the upper area has to be sealed in order to withstand the high amount of cooling water sprayed. Even until today, all attempts to use plastic seals have failed due to the high strand temperatures; spray water remains the only cooling element. However, water cooling has the disadvantage that the scale that enters the bearing seat with the cooling water damages the roller body and races of the roller bearing as the rollers rotate. The casting flux required for an optimum casting process forms hydrofluoric acid on contact with water that quickly corrodes the bearings. These conditions put high demands on the bearings: High temperatures cause the material in the bearing seats to expand considerably, which could subsequently lead to blockages in non-spring-bush roller bearings. The largest possible segment width should be used to support the strand, and this requires bearings that can be installed in the roller thereby restricting the space for complex housings with seals. The high strand temperatures and the consequent need for spray water cooling result in temperature stresses between the side of the roller facing towards the strand and the side facing away from the strand. Depending on the operating conditions in the plant, this situation can lead to bending of the roller, again making high demands on the bearing with respect to operating angle The Eich roller bearing is designed to cope with these demands Thermal behaviour Eich bearings are recognised for their stability under high temperatures. The choice of material and structural design of the bearings allow installation at temperatures of over 200° C. The thermal expansion during the casting process is easily absorbed by the spring bushings / rings installed, and secure seating of the bushings on the shaft or in the bore are guaranteed by the pretension. The bearings can therefore be installed with an optimum press fit. Shiftability Eich BR bearings – standard type – have a sliding action, meaning that they can slide freely in axial direction. Self-locking of the bearings is therefore ruled out. The strand guide roller retains its ability to rotate even with maximum thermal expansion and can therefore provide optimum support for the strand. Cooling and sealing The bearing design adapted to the demands of the production process eliminates the need for additional design measures for cooling and sealing. The lubricant that is supplied via the shaft in the bearing is transported out of the roller via a mechanical labyrinth. The essential function of the lubricant of sealing the bearing is retained. If the Eich bearings are built into the roller, excellent support for the strand shell is ensured by the strand guide roller over practically the whole width of the strand. At the same time, the installation space in the roller with very small bearing diameters can be used to achieve the necessary load ratios. Ingress of foreign matter Eich BR bearings are extremely resistant to damage caused by scale and casting flux residues. A combination of roller bearing steel and special spring steel prevents any breaking out of the bearing components when hard particles are rolled over that could lead to further damage. Controlling wear in this way allows an operational reliability to be achieved that practically rules out unscheduled stoppages. Bending The practically unavoidable bending of the strand guide rollers is compensated by a modified surface profile of the roller bearing body. With cylindrical roller bearings, this value generally cannot exceed 6 angular minutes . Eich BR bearings can withstand constant inclinations in the bearing of 18 angular minutes. Example 1: The introduction of SGC - Segment Gauge Control, a dynamically controlled, hydraulic segment adjustment system for soft reduction, made new demands on the inclinations of the installed bearings. This technical modification permitted better control of the strand shrinkage on cooling and improved the inner quality. Eich bearings can easily accommodate the angles required by the hydraulic control system. Example 2: The introduction of LCR – Liquid Core Reduction – for optimal adaption of the thin slab thickness to the demanded final strip thickness in CSP plants (since the installation of the casting and rolling plant in Bruckhausen) – has further increased the necessity to make the bearings more capable of withstanding angles. A modified roller body form has been used in Eich bearings since 1998. This has since become standard in CSP plants. Older plants are also being gradually converted to the new version of Eich BR bearings. Wear Wear in the bearings generally leads to an uncontrolled increase in backlash. In such cases, the only solution with standard bearings is to replace the complete unit, as the individual components cannot be replaced. The modular system of the Eich BR bearing offers customers the benefits of simple removal and installation even during maintenance. On the other hand it allows the product benefits to be significantly improved and the costs for new investments to be reduced. Worn components (for example, an inner ring subject to heavy loads) can be replaced individually. The profitability of the plant can be improved by installing spring bushing bearings. Product development by Eich – Use of new materials In line with new technologies, such as the development of machines with electro-magnetic stirrers, anti-magnetic strip steels were chosen. Rust-free materials protect the bearings against corrosion from water and casting fluxes in the water. This allows the amount of lubricant to be reduced and enables the changing environmental demands to be satisfied. In slab casters, split water-cooled units serve as a support bearings in the bending and straightening zones that are subject to high static loads. The service life achieves up to 3 million tonnes of production. The bearings are often replaced due to the wear of the roller bodies that support the product – not due to bearing wear. In various conventional slab casting plants, Eich SACRB bearings with dynamically adjusted outer rings and high static load ratios are used in the field of axially sliding floating bearings as counterparts to the self-aligning roller bearing. Plant engineers are currently investigating their use in new plant installations on the basis of their successful experience with Eich SACRB bearings.
|
|
|
|
|