武田机电
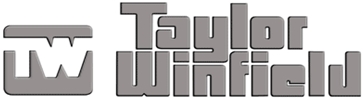
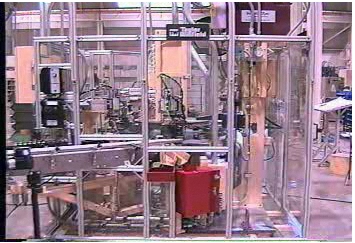
TAYLOR焊机,TAYLOR WINFIELD焊机,TAYLOR WINFIELD焊接机,TAYLOR WINFIELD焊机配件.
TAYLOR-WINFIELD焊机广泛地应用于钢铁行业,从钢铁自动化装备,钢铁成型设备及处理系统,都有TAYLOR的身影,TAYLOR-WINFIELD专注于电阻焊,感应加热焊及电弧焊的研发与生产.
TAYLOR WINFIELD Combination Flash-Butt Welders..... (Drawing) Coil Width: 52" to 100" (1320 mm to 2540 mm) Coil Thickness: .046" to .375" (1 mm to 9.5 mm) Applications: Flash-Butt Welders predominate in Pickle Lines but are also used to advantage in heavy-gauge Coil Preparation, Shot Blasting, Side Trimming and Slitting Lines, and Welded Tube and Pipe Mills. More than 160 Taylor-Winfield steel mill Flash-Butt Welders are in use throughout the world. Description: Flash-Butt Welding is an ultra-fast joining process with fusion occurring over the entire weld area simultaneously. It is the only resistance welding technique in which surface scale has little or no effect on the weld quality and consistency -- a major reason for its use in pickling lines. After trimming, flash-butt welds are as thin as the strip itself and pass readily through subsequent reduction and forming equipment. In most cases, the welds lose their identity and continue on into the consumer product. Combination Flash-Butt Welders are so named because they have a built-in, draw-cut weld trimmer which, in one stroke, removes the excess metal extruded to the surfaces of the strip during the upsetting (forging) portion of the welding cycle. Three types of coil joining Flash Welders are available with Vertical Spacer Bar, with Horizontal Space Bar, and with Integral Shear. A transfer mechanism successively moves the joint to the trimming station and other optional work stations which include an edge punching or notching station and induction post-heating system. The latter minimizes costly strip breakage by tempering the heat-affected zone in alloy steels susceptible to treatment. Welding machines and freestanding flash trimmers can also be furnished as individual units. Automatic welding control systems are available for quickly and accurately resetting all welding parameters when changing strip size or grade. Set-up data can be provided by either computer or operator-controlled selector-switches. All units are available with or without integral shearing mechanisms. Fully automatic designs are now available to meet today's industry requirements. In addition, the popularity of HSLA steels has resulted in Taylor-Winfield's development of a new-generation Flash-Butt Welder incorporating low-voltage/high-current flashing, an oxygen depletion feature, single-step spacer bar, and numerous other design improvements. Non-destructive testing (NDT) equipment can now be offered as an integral part of the combination machine. This feature, using ultrasonic's, can detect inferior welds without increasing the stop time of the entry end of the line. Taylor-Winfield Flash-Butt Welders are the result of over 60 years of experience in building this type of joining equipment. Each is precision-built to exacting tolerances to withstand years o rugged "round-the-clock" operation with minimal maintenance. Many Taylor-Winfield welders delivered in the mid-1930's are still generating profits for their owners.
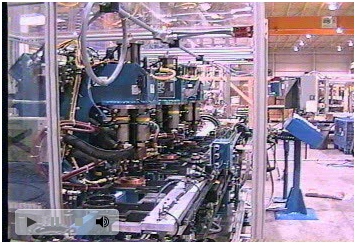
TAYLOR WINFIELD TW: Resistance-Welding RESISTANCE WELDING POWER CHART PRESS WELDER |FLASH-BUTT WELDER | BENCH WELDER |SEAM WELDER | ROCKER ARM WELDER | BANDSAW BLADE WELDER PRESS WELDERS INV-1, click here for more information Bench Type - Invertor or AC Spot/Projection Welder This inverter welding head is so revolutionary we had to give it a special name. Atop the low inertia ram you'll find a patented accelerator that gives the "Blue Goose" the best follow-up action in the welding industry. This makes it an ideal machine for cross-wire welding, and other spot and projection welding applications. It lays down low impact, high-speed welds with exceptional repeatability andvirtually no deflection. EBB-3, click here for more information Our best seller, the floor model EBB-3, RWMA Size 0, incorporates all the features of our larger models making thisthe lowest cost, most versatile piece of equipment in our resistance welder line. These welders are strong, compact, efficient and capable of spot or projection welding. Crafted of high quality materials with T-W dependability. ENE, click here for more information ENE, RWMA Size 1 gives you simplified versatility to meet your more complex welding needs. It allows you to switch from spot welding to projection welding with an absolute minimum of changeover time. Taylor-Winfield quality is reflected throughout. Units are constructed of the finest materials by highly skilled craftsmen. We maintain an extensive inventory of replacement parts to assure maximum operation. In-stock components can ship within 24 hours of order receipt. EVOLUTION, click here for more information Evolution 1, RWMA Size 1 gives you simplified versatility to meet your more complex welding needs. It allows you to switch from spot welding to projection welding with an absolute minimum of changeover time. Taylor-Winfield quality is reflected throughout. Units are constructed of the finest materials by highly skilled craftsmen. We maintain an extensive inventory of replacement parts to assure maximum operation. In-stock components can ship within 24 hours of order receipt.. ZDN, click here for more information The ZDN-TQ Series of Economical Spot/Projection Welders offers you simplified versatility to meet your parts production and resistance welding need. Switch from spot to projection welding with minimum changeover time. EPE, click here for more information Single Phase ? Press Type EPE, RWMA Size 3 gives you simplified versatility and dependability. ? It allows you to switch from spot welding to projection welding with an absolute minimum of changeover time. ? Taylor-Winfield quality is reflected throughout. ERE, click here for more information Single Phase ? Press Type One of our most rugged welders, the ERE, RWMA Size 2, gives you simplified versatility and dependability, allowing you to switch from spot to projection welding with an absolute minimum of changeover time. Taylor-Winfield quality is reflected throughout. In addition, we stock a complete inventory of replacement parts and in-stock components can be shipped within 24 hours of order receipt. When you buy from Taylor-Winfield, you get sound technical advice, competent service and continued performance backed by single source responsibility. RPW SERIES click here for more information Heavy Duty Steel Frame Construction, All Copper Secondary Components, Adjustable Upper and Lower Horns, Adjustable Upper and Lower Electrode Holders, Electrodes and Platens Machined to, RWMA Dimensional Specifications BENCH WELDERS EB-00click here for more information ? Precision straddle ball bushing and dual cam roller ram guide system of long term electrode alignment and minimum dynamic friction. ? Precision calibrated pre-compressed spring weld force system with micrometer readout scale for maximum reset ability. ? Weld force firing switch to assure application of electrode force before current flow initiation. ? Low inertia upper electrode ram structure for superior follow-up on extremely short weld times. ? Adjustable-rotatable horns for versatile electrode configuration capability. ? High strength socket head cap screw electrode clamping hardware to resist head stripping in repeated use. ? Transformer cable mounting studs to isolate electrodes from cable magnetic impulse. ? With accelerator foot treadle and pull chain. ? Lever-operated for minimum operator fatigue. EB-1, EBA 1 1/2 click here for more information ? These bench mounted welders consist of a cast main frame mounted on a tubular support column. The column passes through a hole in the bench top and is supported by the welder base. This provides vertical adjustment of the lower horn and upper electrode holder. Height of machine above bench top is also adjustable. ? The upper electrode is attached to a copper alloy holder; a flexible copper band connects the upper holder to the rear terminal which provides the means for attachment of the welding transformer cable. ? The lower horn holds the lower electrode in a vertical positions or at desired angular positions. The horn may be swung to either side and is adjustable in or out. The lower horn has a terminal pad for attachment of the transformer cable. ? A precision type firing switch is actuated by compression of the weld force spring which assures that proper weld force is applied prior to control firing. ? Low friction bearings and low inertia of moving parts assures high quality welding on critical jobs. EB-1 Operation: (Foot Operated Only) EB-1 welder an operating rod, which moves up and down through the tubular column, is attached to a lever in the welder frame which in turn transmits vertical movement to a non-rotating outer quill. When the operating rod is pushed upward, the outer quill is moved downward until the upper electrode contacts the work. This upper electrode is attached to a low inertia inner quill operating in oilite bushings. A downward pressure is exerted on this inner quill by a graduated pressure spring which determines the actual welding force.. By means of mechanical linkages maximum welding force with very little muscular effort is obtained. Such linkage action permits rapid approach of the upper electrode to the work, controlled deceleration and contact on the work without impact. The foot operating mechanism consists of a swinging type treadle, adjustable to individual leg length and angle requirements. A bicycle type pedal permits natural leg motion for high-speed production. EBA-1-1/2: Operation: (Air Operated) In the EBA-1-1/2 welder the upper electrode is clamped to an operating ram having hardened and ground guide surfaces. These surfaces are contacted by sealed adjustable antifriction roller bearings, assuring a smooth low friction vertical motion of the ram, necessary for precise welder operation. These welders are ideal for projection welding when fitted with tooling platens. The air operating mechanism is mounted on top of the welder frame and consist of an air cylinder with a screw adjustment for setting the stroke of the welder head. It is also equipped with an air filter, oil fog lubricator, solenoid operated 4-way air valve and exhaust muffler. A foot switch is provided to initiate the welder operation. A foot operating mechanism is available on request as a special extra cost option. INV-1 Blue Goose click here for more information. Bench Type - Invertor or AC Spot/Projection Welder This inverter welding head is so revolutionary we had to give it a special name. Atop the low inertia ram you'll find a patented accelerator that gives the "Blue Goose" the best follow-up action in the welding industry. This makes it an ideal machine for cross-wire welding, and other spot and projection welding applications. It lays down low impact, high-speed welds with exceptional repeatability andvirtually no deflection. FLASH-BUTT WELDERS click here for more information. Flash-Butt welding is a process designed to produce a forge-type butt weld between two metal pieces of similar shape. It is used to join ends of rods, bars, strips, rings, tubes, forgings and fittings. The pieces to be joined are clamped in fixtures which are connected to the secondary of a welding transformer. One of the clamp fixtures is mounted on a slide which is programmed to move toward the stationary clamp at a controlled rate. During this movement the transformer is energized and as the workpieces touch, welding current flows. This flash process generates heat in the workpieces. At the proper temperature the slide driving mechanism rapidly accelerates, forging the work pieces together to form a joint essentially as strong as parent metal without the aid of any filler material. This "upsetting" action forces impurities out of the weld zone. Thus the inner weld metal is sound and free of oxides or cast metal. SEAM WELDERS click here for more information. The main frame of these seam welders is of heavy, rigidly reinforced welded steel construction for a minimum of mechanical deflection but a maximum of accessibility and neat appearance. The lower conductor support or knee is a heavy steel fabrication keyed to the frame for accurate vertical adjustment. The upper conductor is insulated from the frame, while the lower conductor is grounded to the frame, therefore work support tables or conveyors can also be grounded.
TAYLOR WINFIELD Assembly Systems: For Your Process - For Your Industry To manufacturers whose process involve parts handling and any size assemby or sub-assembly, The Taylor-Winfield Assembly product line offers valuable automation technology. The industries we serve range from appliance to automotive and all types of transportation, small products and hardgoods to electrical and electronics. We provide general automation for mechanical or electro-mechanical assembly, as well as systems for industries with specialized processes and highly sensitive environments. For Systems Designed and Built to Your Needs Each Taylor-Winfield system is custom-designed and built to the requirements of the specific assembly process. System components - from new designs to selected existing solutions - are properly integrated, and their quality assures precise, reliable performance in these diciplines: Assembly - Robotic transfer arms are integrated for more complex, intricate operations. Joining processes such as multiple welds and the application of coatings and adhesives are common examples of their functions. All are programmable and selected for their proven dependability and ease of operation. Joining and fastening equipment for the methods you use - from welding, driving screws and rivets to adhesive bonding can also be incorporated. Indexing - Rotary and linear index systems are configured and integrated to move you workpieces smoothly and reliably from station to station. Parts loading and unloading equipment can be provided as part of the production line or for specific stages of the assembly process. Diagnostics T-W has designed custom systems with sophisticated diagnostics that assist your machine operators and maintenance technicians with the operation of the equipment. We have also utilized special software packages that include such features ass Statistical Process Control (SPC), Event Detectors, Data Logger, Reporting, Trending Network and Alarming Synchronous Systems, Rotary and Linear We design and build the configuration that keeps your workpieces moving, work station to work station. It's a well crafted component with assured quality performance, and just part of the whole system integrity that makes T-W automation a sound, reliable decision for you. Non Synchronous Systems Manual stations and automatic stations can be built on linear tracks as well as cross transfers. These systems are especially suitable for the cost effective assembly of products in series production. Furthermore, it becomes possible to work in steps by adding automated cells to theassemblly process at a later date. Non-synchronous systems gain an additional advantage over synchronous systems from thestandpoint that all of the workstations are independent of each preceding and following stations. Our high standards in robotic transfer arms are paramount to providing the best automated assembly systems in the industry. This is a position that we are commited to maintaining, by bringing you the valuable solutions you need, now and in the future. Quality Control Automatic vision systems are available for on-line inspection of parts, small assembiles or assemblies. Reject parts sensors and handling equipment can also be provided to signal and/or remove problem parts from the line. Tracking systems - bar code, mechanical and software driven - for parts and assemblies are integrated as required. Self diagnostic functions can be includedfor monitoring and display of operating status and conditions. System Automation Your Taylor-Winfield system can be semi-automatic or fully automatic according to your utilization of human resources, economics, your process and product needs. For Production Flexibility and Factory Floor Durability Importantly, Taylor-Winfield systems offer you flexible automation - for the way you must manufacture today. Your system can be designed for efficient on-site adjustment to changing project parameters and production rates.We will integrate it into your existing lines or develop it as part of a new line, and can design it to meet our CIM requirements A valuable advantage of all Taylor-Winfield systems and components is their ability to withstand the rigors of production and plant environment. Your system is fully tested in our manufacturing facilities and yours to make certain. Our reputation for solidly reliable equipment backs your system. And of course, direct Taylor-Winfield support and service is easily accessible and prompt. Call On Us. We're Here to Work With You. First, we work directly with your engineering and product design departments to gain an in-depth understanding of your particular needs and goals. We'll discuss feasible, on-target solutions and submit a complete proposal. Then, we'll design your systems, putting our capabilities, experience - our high standards - to work for you. With Taylor-Winfield, you'll find a responsible, responsive supplier, committed to your needs from our first consultation to delivery of your systems.
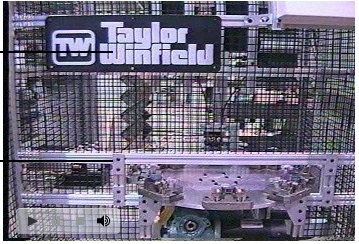
TAYLOR WINFIELD Ther-Monic Induction Heating Power Supplies Ther-Monic Products New Products Choose by Frequency and Power Applications Induction Heating Applications TW Automation Work Stations, Scanners, Automated Systems Support Services Copper Products, Spare Parts,Field Service Development Laboratory
TAYLOR WINFIELD Arc Welding We have developed a wide variety of arc welding solutions for specificapplications. Using our more than 75 years of arc welding experience we can developMig, Tig, Plasma and automated arc welding solutions for virtually any application. We can also help you determine the best process for your application and supply the right tooling package, controls and work handling equipment for your job.
TAYLOR焊机,TAYLOR WINFIELD焊机,TAYLOR WINFIELD焊接机,TAYLOR WINFIELD焊机配件